Table of contents
隐藏
1. Introduction: The Critical Role of HDPE Tees in Modern Pipe Systems
- Explain what HDPE tees are and their purpose: connecting three pipe sections in a “T” configuration for fluid distribution.
- Highlight common challenges with low-quality tees: leaks, pressure failures, and corrosion, leading to downtime and costly repairs.
- Position high-quality HDPE tees as a solution for efficiency, safety, and long-term durability in industrial, municipal, and agricultural applications.
2. Key Features of Efficient & Secure HDPE Tees
- Premium Material Advantages:
- HDPE (High-Density Polyethylene): Lightweight, non-corrosive, and resistant to chemicals, UV rays, and abrasion (ideal for harsh environments like wastewater or mining).
- High Pressure Ratings: SDR11/SDR17.6 options for systems requiring 10 bar–25 bar pressure tolerance (meets ISO 4427 and ASTM D2683 standards).
- Temperature Resistance: Operates reliably from -40°C to 60°C, making it suitable for cold climates and moderate-temperature fluids.
- Design for Optimal Flow & Safety:
- Smooth Bore Design: Minimizes turbulence and pressure loss, improving system efficiency by up to 15%.
- Integral Socket or Electrofusion Ends: Ensures leak-proof joints when welded correctly, reducing installation errors.
- Uniform Wall Thickness: Tested via laser scanning to prevent weak points and ensure consistent structural strength.
3. Where to Use HDPE Tees: Diverse Industrial & Commercial Applications
- Municipal Water & Wastewater Systems:
- Safe for potable water distribution (NSF 61-certified materials) and sewage networks (resistant to biofouling and aggressive chemicals).
- Industrial Fluid Handling:
- Chemical processing plants, oil & gas pipelines, and manufacturing facilities requiring corrosion-resistant fittings.
- Agricultural Irrigation:
- Lightweight design simplifies installation in remote fields; UV-stabilized options extend lifespan in outdoor environments.
- Renewable Energy:
- Geothermal systems and biogas pipelines, where durability and leak prevention are critical.
4. How to Avoid Common Pitfalls: 5 Tips for Selecting High-Quality HDPE Tees
- 1. Check Material Certifications:
- Look for ISO 9001-manufactured products with third-party testing (e.g., SGS, Bureau Veritas) for melt flow index (MFI) and tensile strength.
- 2. Verify Pressure & Size Compatibility:
- Ensure the tee’s SDR (Standard Dimension Ratio) matches your pipeline’s pressure requirements (e.g., SDR11 for high-pressure, SDR17.6 for low-pressure systems).
- Available sizes: DN20 to DN1200 (custom sizes for special projects).
- 3. Assess Welding Compatibility:
- Electrofusion tees should have embedded heating coils with clear manufacturer guidelines for welding parameters (voltage, time, cooling period).
- 4. Avoid Recycled Material Red Flags:
- Low-cost tees may use recycled HDPE with inconsistent properties; request material composition reports to confirm 100% virgin resin.
- 5. Test for Impact Resistance:
- Drop-test samples at low temperatures to ensure they won’t crack in freezing conditions (critical for outdoor installations).
5. Why Partner with a Reputable HDPE Tee Manufacturer?
- Factory-Direct Benefits:
- Eliminate middlemen costs while gaining access to strict quality control (e.g., 100% pressure testing before shipment).
- Customization options: colored tees for easy system identification, anti-static coatings for gas applications, or branded packaging for distributors.
- Technical Support & Logistics:
- Free welding guides and on-site training for large projects.
- Global shipping with DDP (Delivered Duty Paid) options and short lead times (7–15 days for standard orders, 3–4 weeks for custom designs).
- Case Study: How a Mining Company Reduced Leaks by 90%
- A Chilean copper mine switched to electrofusion HDPE tees with SDR11, eliminating corrosion-related failures in acidic wastewater lines.
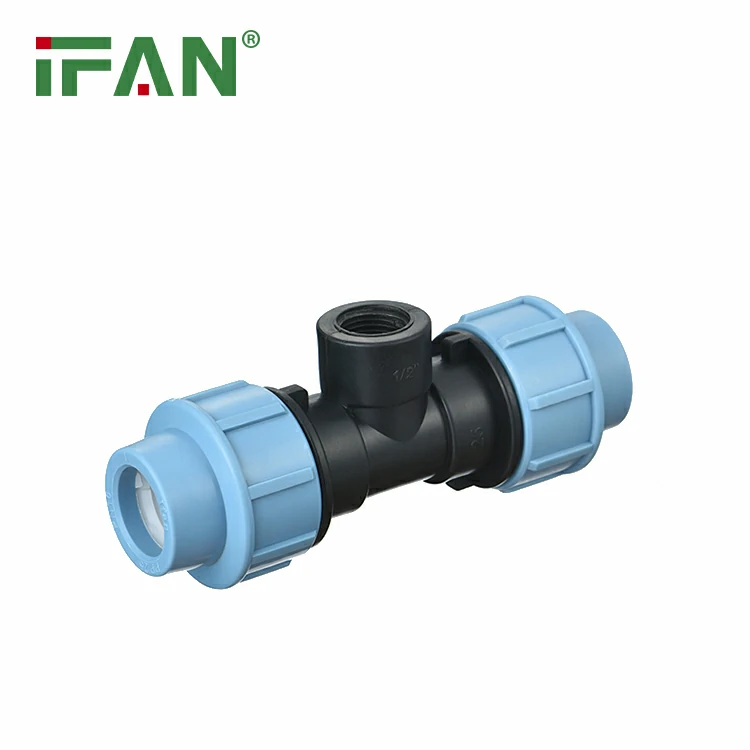
6. The Step-by-Step Guide to Purchasing HDPE Tees
- Step 1: Define Your System Requirements:
- List fluid type (water, gas, chemicals), operating pressure/temperature, pipe diameter, and connection type (socket, electrofusion, butt-weld).
- Step 2: Request Samples & Documentation:
- Test samples for fit and material quality; review COA (Certificate of Analysis) and welding procedure specifications (WPS).
- Step 3: Compare Suppliers:
- Evaluate MOQs (low minimums like 100 units for small projects), warranty periods (5–10 years for structural integrity), and after-sales support.
7. Call to Action: Secure Your Pipeline with Premium HDPE Tees
- Encourage readers to:
- Visit your website to explore our full range of HDPE tees (link to product page with size/price filters).
- Download a free checklist: “10 Questions to Ask Your HDPE Tee Supplier” (gate with email capture for lead nurturing).
- Contact our team for a personalized quote, including free CAD drawings and a complimentary welding tool demo.
Conclusion: Invest in Efficiency and Safety with HDPE Tees
Reinforce that HDPE tees are not just fittings—they’re the backbone of reliable pipe systems. Prioritize quality to avoid downtime, leaks, and safety risks. Partner with a manufacturer who combines technical expertise, customization capabilities, and global logistics to meet your project’s unique needs.
Recent Comments