Table of contents
隐藏
1. Introduction: The Critical Role of HDPE Pipe Fittings in Modern Infrastructure
- Explain the growing use of HDPE (high-density polyethylene) in pipelines for its durability, corrosion resistance, and flexibility.
- Highlight a common pain point: poor-quality socket fittings leading to leaks, installation delays, or system failures.
- Position high-quality HDPE pipe fittings as the solution to reduce socket-related issues, emphasizing long-term cost savings and performance.
2. Why “Reduce Socket” Matters: Common Problems with Low-Quality Fittings
- Leakage Risks: Inferior materials or improper socket design causing joint failures under pressure.
- Installation Inefficiency: Ill-fitting sockets requiring rework, increasing labor and project timelines.
- Limited Longevity: UV degradation, chemical corrosion, or stress cracking in non-engineering-grade HDPE.
- Safety Concerns: Non-compliant fittings risking environmental contamination or system downtime.
3. Key Features of High-Quality HDPE Pipe Fittings for Socket Reduction
- Premium Material Composition:
- Virgin HDPE resin (not recycled) for superior impact resistance, tensile strength, and chemical tolerance (e.g., ASTM D3350, ISO 4427 compliance).
- UV-stabilized formulations for outdoor/underground use without degradation.
- Precision Engineering for Perfect Socket Joints:
- Uniform wall thickness and dimensional accuracy (ISO 11672) to ensure tight, fusion-weldable sockets.
- Smooth internal surfaces to minimize flow resistance and sediment buildup.
- Designs Optimized for Easy Installation:
- Socket ends with chamfered edges for hassle-free alignment during fusion or electrofusion welding.
- Standardized sizes (DN15-DN1200) compatible with global industry standards (SDR11, SDR17.6).
- Quality Assurance & Testing:
- 100% pressure testing (up to 25 bar) and visual inspections to eliminate defects.
- Certifications: CE, SGS, WRAS (for potable water applications), ensuring compliance in target markets.
4. Applications: Where High-Quality HDPE Fittings Shine
- Water & Wastewater Systems: Reliable socket connections in municipal pipelines, sewage treatment plants, and irrigation networks.
- Oil & Gas Infrastructure: Corrosion-resistant fittings for offshore platforms, chemical pipelines, and gas distribution.
- Industrial Projects: Handling aggressive fluids in manufacturing, mining, or pulp/paper industries without socket degradation.
- Renewable Energy: Use in geothermal systems, solar panel cooling loops, and biogas installations requiring low-maintenance joints.
- Case Study Insight: How a Southeast Asian utility company cut repair costs by 40% with precision-engineered HDPE socket fittings.
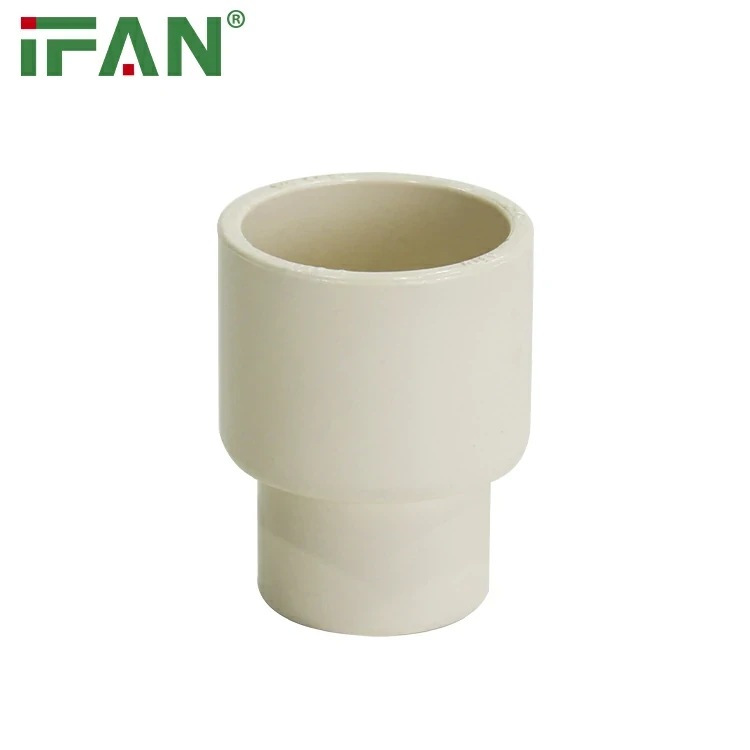
5. How to Choose the Right HDPE Pipe Fittings Supplier
- 1. Prioritize Material Transparency:
- Ask for material datasheets, resin sources (e.g., ExxonMobil, Dow Chemical), and recycling rates (avoid suppliers using >30% recycled material for critical applications).
- 2. Evaluate Manufacturing Expertise:
- Look for suppliers with in-house extrusion and molding capabilities (ensures tight quality control over socket dimensions).
- Check for automated production lines and robotic welding equipment (reduces human error in socket formation).
- 3. Customization Options:
- Does the supplier offer bespoke socket designs (e.g., non-standard angles, reinforced sockets for high-pressure zones)?
- Low MOQs for small projects or trial orders (ideal for contractors testing new suppliers).
- 4. After-Sales Support:
- Technical guidance on socket welding procedures (e.g., fusion temperature: 210-230°C for HDPE).
- Warranty coverage (e.g., 5+ years for manufacturing defects) and quick replacement for faulty fittings.
6. Ready to Buy? Your Step-by-Step Guide to Reducing Socket Issues
- Step 1: Define Your Project Needs:
- Specify operating pressure, temperature, fluid type, and installation method (fusion welding vs. mechanical joints).
- Step 2: Request Samples & Test Socket Fit:
- Validate socket alignment with your existing pipes; check for snug fits without excessive force.
- Step 3: Compare Suppliers on Quality, Not Just Price:
- A 10% cheaper fitting may cost 50% more in repairs later—prioritize suppliers with proven track records in your industry.
- Step 4: Partner for Long-Term Success:
- Look for suppliers offering inventory management (just-in-time delivery) and engineering support for complex projects.
7. Call to Action: Upgrade to High-Quality HDPE Fittings Today
- Recap the benefits: fewer socket issues, lower maintenance, and enhanced system reliability.
- Direct readers to take action:
- Visit [Your Website URL] to browse certified HDPE pipe fittings with precision-engineered sockets.
- Download our free guide: “10 Tips for Perfect HDPE Socket Welding” (offer a lead magnet for email sign-ups).
- Request a quote for custom socket designs or bulk orders (include a prominent contact form link).
Conclusion: Invest in Quality to Eliminate Socket-Related Headaches
- Reinforce that high-quality HDPE fittings are a strategic investment, not an expense.
- Position your brand as a trusted partner for durable, engineered solutions:
“Don’t let poor socket fittings compromise your project. Choose HDPE pipe fittings designed for precision, performance, and peace of mind.”
Recent Comments