1. Introduction
In the competitive pipeline market, customization has become a key differentiator. At IFAN Pipeline, we understand that every project has unique requirements. This blog post will guide you through our customization process for PPR pipes, highlighting how we ensure precision, efficiency, and compliance with international standards.
2. Initial Consultation & Requirement Analysis
2.1 Dedicated Account Manager
Your customization journey starts with a free consultation with our experienced account managers. They will:
- Listen to your project specifications (dimensions, pressure ratings, application scenarios)
- Provide technical advice on material selection (PPR Type 1/Type 2)
- Discuss special requirements (e.g., UV resistance, thermal insulation)
2.2 RFQ (Request for Quotation) Form
For complex projects, we recommend submitting our online RFQ form. This helps us:
- Capture detailed parameters (OD/ID, wall thickness, color)
- Clarify performance standards (EN 12201, NSF 61)
- Identify bulk discount opportunities
3. Engineering & Design Validation
3.1 3D Modeling & Prototyping
Using advanced CAD software, our engineers create:
- 3D renderings for visual approval
- Customized fittings (elbows, tees, valves)
- Pressure test simulations
3.2 Sample Production
Before mass production:
- A pilot batch is produced
- Undergoes rigorous testing (burst pressure, chemical resistance)
- Delivered to you for final approval
4. Production & Quality Control
4.1 ISO 9001 Certified Manufacturing
Our state – of – the – art facility ensures:
- Precision extrusion of PPR resin
- Custom printing (logos, batch codes)
- Real – time monitoring of production parameters
4.2 Third – Party Inspections
For large orders, we offer:
- SGS/Intertek on – site audits
- Material composition verification
- Leakage detection using ultrasonic technology
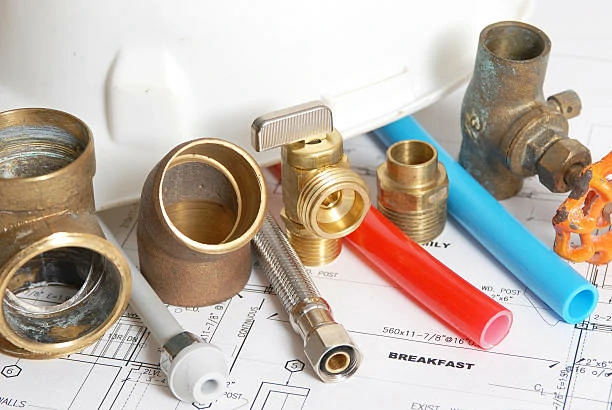
5. Logistics & After – Sales Support
5.1 Global Shipping Solutions
We provide:
- Door – to – door logistics via DHL/FEDEX
- Containerized sea freight with tracking
- Customized packaging (palletized, labeled)
5.2 Post – Installation Support
Our commitment continues after delivery:
- On – site technical assistance
- 2 – year warranty on customized products
- Free replacement for defective items
6. Case Studies: Customization in Action
6.1 Hotel Renovation Project
Challenge: Required non – standard PPR pipes for high – temperature geothermal water systems
Solution: Customized PPR – CT pipes with enhanced heat resistance
Result: Reduced maintenance costs by 30% over 5 years
6.2 Municipal Water Project
Challenge: Large – diameter pipes with anti – microbial coatings
Solution: 800mm PPR pipes with silver – ion infused liners
Result: Compliance with WHO drinking water guidelines
7. Why Choose IFAN’s Customization Services?
- 15+ Years of Expertise: Specialized in B2B pipeline solutions
- Flexible MOQ: From 100 meters to bulk orders
- Multi – Language Support: English, Spanish, Arabic speaking teams
- Rapid Turnaround: 7 – 14 days for sample production
8. FAQs about Customization
- Q: Can I customize pipe colors?
A: Yes! Choose from RAL color chart or provide your own Pantone code. - Q: Do you handle custom fittings?
A: Absolutely! We produce bespoke adapters and flange connections. - Q: What certifications do your customized products carry?
A: All products meet EN 12201, NSF 61, and GB/T 18742 standards.
9. Conclusion
At IFAN Pipeline, our end – to – end customization process combines technical expertise with customer – centric service. Whether you need special coatings, unique dimensions, or branded solutions, we turn your specifications into high – performance PPR pipes.
Ready to start your project?
Visit ifanpro.com to request a quote or contact our team directly. Let’s build the perfect pipeline solution together!
Recent Comments