Table of contents
隐藏
1. Introduction: The Critical Role of HDPE End Caps in Industrial Pipe Systems
- Explain what HDPE end caps are and their primary function: sealing pipe ends to prevent contamination, leaks, or debris ingress.
- Highlight common challenges with low-quality end caps: brittle fractures, poor chemical resistance, and inadequate sealing under pressure.
- Position factory-direct high-quality HDPE end caps as a cost-effective solution for durability and safety in industries like water supply, gas distribution, and construction.
2. Key Features of Premium HDPE End Caps: What “High Quality” Really Means
- Material Purity & Grade:
- 100% virgin HDPE (not recycled) for superior impact resistance, chemical tolerance, and UV stability (e.g., PE100 or PE80 resin compliant with ISO 4427).
- Resistance to aggressive chemicals (acids, alkalis) and extreme temperatures (-40°C to 60°C for long-term use).
- Precision Manufacturing for Secure Sealing:
- Smooth inner/outer surfaces to eliminate stress points and ensure tight fusion with HDPE pipes (compatible with butt-welding or electrofusion methods).
- Uniform wall thickness (tested via laser scanning) to withstand high pressure (up to 16 bar for PE100-grade caps).
- Certifications & Standards:
- Compliance with global norms: ASTM D3350 (USA), EN 12201 (EU), or GB/T 19472.1 (China).
- Third-party testing reports for tensile strength (≥26 MPa), elongation at break (≥350%), and carbon black content (2.0–2.5% for UV protection).
3. Where to Use HDPE End Caps: Diverse Industrial Applications
- Water & Wastewater Systems:
- Sealing unused pipe ends in municipal pipelines, sewage treatment plants, or irrigation networks.
- Case example: A Middle Eastern desalination plant used UV-stabilized HDPE end caps to prevent seawater corrosion in outdoor pipelines.
- Gas Distribution:
- Temporary or permanent sealing of natural gas or biogas pipes during installation or maintenance (ensures no methane leakage).
- Construction & Infrastructure:
- Industrial Processing:
- Isolating sections of chemical pipelines during maintenance or system upgrades (resistant to solvents like methanol or hydrochloric acid).
4. How to Avoid Low-Quality End Caps: 5 Key Selection Criteria
- 1. Material Sourcing & Transparency:
- Red flag: Suppliers who cannot provide material certificates or admit to using recycled HDPE.
- Ask for a COA (Certificate of Analysis) to verify resin grade and additive composition.
- 2. Manufacturing Process:
- Premium caps use injection molding with high-pressure machines (ensures uniform density) vs. low-cost extrusion methods (risk of voids).
- 3. Design Compatibility:
- Check for compatibility with your pipe type (standard HDPE, MDPE, or special blends) and connection method (socket, butt-weld, or threaded options).
- 4. Testing Protocols:
- Ensure suppliers conduct hydrostatic pressure tests, cold impact tests, and long-term creep rupture tests (critical for high-pressure systems).
- 5. Supplier Reputation:
- Look for factories with ISO 9001 certification, long production history (5+ years), and client reviews from industries like oil & gas or water utilities.
5. Why Buy Factory-Direct HDPE End Caps? 4 Unmatched Advantages
- 1. Cost Efficiency Without Compromise:
- Eliminate distributor markups: Factory prices are typically 20–30% lower than retail, especially for bulk orders (MOQs as low as 100 units for standard sizes).
- 2. Customization for Unique Needs:
- Tailored dimensions: OD ranging from 20mm to 1200mm, with options for thickened walls (for extreme pressure) or anti-static coatings (for gas applications).
- Branding: Embed logos or part numbers for easy inventory management (ideal for contractors).
- 3. Stringent Quality Control:
- In-house labs for material testing and 100% visual inspection before packaging.
- Example: A Chinese factory uses automated X-ray machines to detect internal defects in every batch.
- 4. Global Logistics Support:
- Fast lead times (7–15 days for standard orders) and flexible shipping (DHL for samples, sea freight for bulk, with DDP options for hassle-free customs).
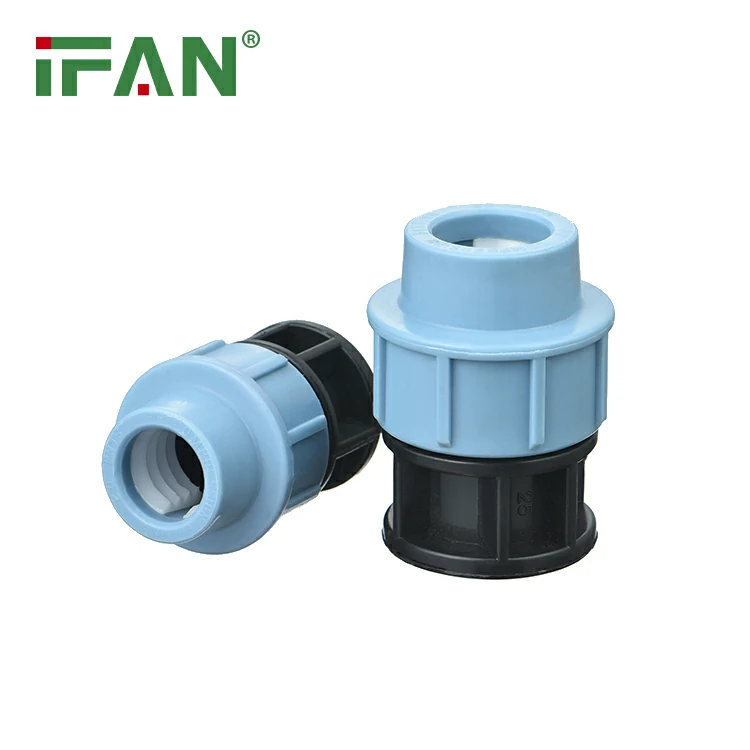
6. Step-by-Step Guide: How to Purchase the Right HDPE End Caps
- Step 1: Define Your Requirements:
- Specify pipe outer diameter (OD), pressure rating, application environment (underground, above-ground, or submerged), and quantity needed.
- Step 2: Request Samples & Documentation:
- Test samples for fit, flexibility, and resistance to your project’s specific chemicals/temperatures.
- Review factory audit reports (if available) to assess production capabilities.
- Step 3: Compare Quotes & Terms:
- Factor in not just price, but also warranty (look for 5+ years), after-sales support, and customization fees (if applicable).
- Step 4: Place an Order with Confidence:
- For first orders, start with a small batch to validate quality before scaling up.
7. Call to Action: Secure Your Pipe Systems with Factory-Grade HDPE End Caps
- Encourage readers to:
- Visit your website to browse standard sizes (link to HDPE end cap product page) and request a free sample kit.
- Download a checklist: “10 Questions to Ask Your HDPE End Cap Supplier” (gate with email capture for lead generation).
- Contact your team for a customized quote, including CAD drawings for non-standard designs or bulk pricing for projects over 500 units.
Conclusion: Invest in Factory Quality for Leak-Free, Long-Lasting Pipe Sealing
Reinforce that HDPE end caps are not just accessories but critical components for system integrity. Position your factory as a reliable partner with expertise in material science, precision manufacturing, and global supply—ideal for projects where failure is not an option. End with a strong reminder that choosing factory-direct ensures both quality and cost-efficiency, making it a smart decision for any industrial or infrastructure project.
Recent Comments