Installing piping systems for chemical applications requires a high level of precision, material compatibility, and long-term durability. Among the various piping options, PPR (Polypropylene Random Copolymer) pipes are increasingly used in chemical industries due to their excellent resistance to corrosion, chemical leaching, and high temperatures.
This guide walks you through the correct installation process of PPR pipes in chemical systems, helping you achieve safety, efficiency, and compliance.
Why Use PPR Pipes in Chemical Systems?
Before diving into the installation process, it’s important to understand why PPR pipes are ideal for chemical environments:
- Chemical resistance: Suitable for many acids, alkalis, and salts
- Non-toxic and corrosion-free: No scaling or rusting over time
- Lightweight and easy to handle: Reduces labor costs
- Fusion welding technology: Creates strong, leak-free joints
- High temperature and pressure tolerance
ifanpro, a leading PPR pipe supplier from China, offers chemical-grade PPR pipes specifically engineered for such demanding environments.
Step-by-Step Guide: Installing PPR Pipes for Chemical Applications
1. Plan the Piping Layout
Before installation, develop a detailed piping layout drawing that includes:
- Pipe diameters and lengths
- Flow direction
- Support points
- Fittings (elbows, tees, valves)
- Safety and maintenance access points
This ensures efficient flow and minimizes pressure drop or dead zones.
2. Prepare Tools and Equipment
Ensure the following tools are ready:
- Pipe cutter or shear
- PPR welding machine (fusion tool)
- Chamfering tool
- Measuring tape and marker
- Pipe support brackets
- Protective gloves and safety goggles
Safety is critical when handling chemicals, so personal protective equipment (PPE) is essential.
3. Cut and Chamfer the Pipes
Use a pipe cutter to cut the PPR pipe to the required length. Then, use a chamfering tool to bevel the end of the pipe. This step helps in achieving a smooth and secure fusion weld.
Tip: Always cut pipes square to ensure perfect alignment during fusion.
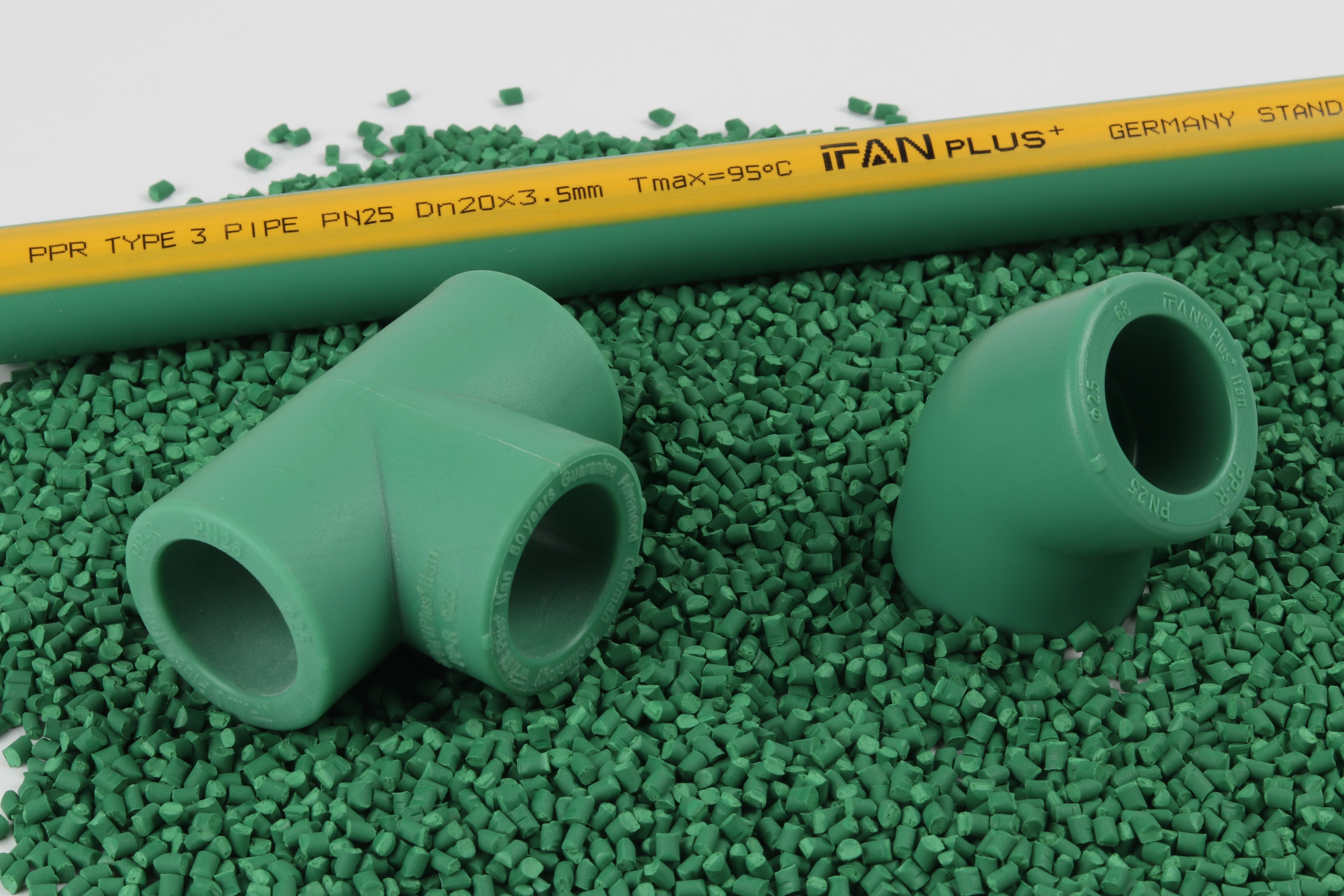
4. Fusion Welding Process
Fusion welding (also called socket fusion) is the standard method for joining PPR pipes:
- Heat the welding tool to the recommended temperature (typically around 260°C / 500°F)
- Insert the pipe and fitting into the sockets simultaneously
- Hold for a few seconds (as per pipe size)
- Remove and immediately press them together
- Hold the joint in place to cool for 20–30 seconds
This creates a homogeneous joint that’s as strong as the pipe itself—ideal for chemical resistance and leak prevention.
5. Install Pipe Supports and Clamps
Install pipe brackets or hangers to secure the pipeline at regular intervals. For chemical systems, avoid metal supports that may corrode; use plastic or coated brackets.
- Horizontal piping: Support every 50–75 cm (depending on pipe diameter)
- Vertical piping: Provide supports at each floor level
This prevents sagging, vibration, or mechanical stress on the joints.
6. Pressure Testing
Once installation is complete, conduct hydrostatic pressure testing to check for:
- Leaks
- Joint integrity
- Pressure holding capacity
Ensure that the testing fluid is compatible with the pipe and the chemical application. If using water, ensure the pipes are dried before introducing chemicals.
7. Chemical Compatibility Check
Before starting the system, double-check that the chemical being transported is compatible with PPR. Most non-oxidizing acids, alkalis, and saline solutions are safe, but consult chemical compatibility charts or request data from your pipe supplier.
At ifanpro, we offer custom technical support to help you verify compatibility and choose the right pipe grade.
Final Tips for Success
- Avoid sharp bends or over-tightening fittings
- Use color coding or labeling for different chemical lines
- Keep proper documentation of pipe specifications and test reports
- Train your installation team on safety and fusion best practices
Conclusion
Proper installation of PPR pipes in chemical systems is crucial for safety, performance, and longevity. By following the correct procedures—from planning and cutting to welding and testing—you ensure a reliable system that meets industrial standards.
Looking for high-quality chemical-resistant PPR pipes and expert support? Visit ifanpro.com to explore our product range and contact our technical team for tailored solutions.
Commentaires récents