PPR (Polypropylene Random Copolymer) pipe fittings serve the same fundamental purpose across continents, yet significant differences exist between American and European markets. Understanding these variations helps contractors, engineers, and facility managers make informed purchasing decisions.
Standards and Certifications
European PPR fittings follow strict EN ISO 15874 standards. These regulations govern material composition, pressure ratings, and temperature resistance. The certification process requires rigorous testing under controlled conditions.
American fittings typically comply with ASTM standards, particularly ASTM F2389. NSF certification ensures drinking water safety. IAPMO approval adds another layer of quality assurance for plumbing applications.
Pressure and Temperature Ratings
European PPR fittings commonly handle higher pressure ratings. Standard European fittings operate at PN20 (20 bar) or PN25 (25 bar) pressure levels. Temperature resistance reaches 95°C for continuous operation.
American fittings focus on different pressure classifications. SDR ratings (Standard Dimension Ratio) determine wall thickness and pressure capacity. Most US fittings operate effectively at 160-180°F maximum temperatures.
Connection Methods and Design
European manufacturers emphasize heat fusion welding techniques. Socket fusion remains the primary connection method. Electrofusion options provide alternatives for specific applications.
American PPR systems incorporate more threaded connections. Transition fittings accommodate existing copper or PVC infrastructure. This flexibility suits renovation projects in older buildings.
Material Composition Differences
European PPR compounds often include advanced stabilizers. UV resistance receives particular attention for exposed installations. Antioxidants extend service life in harsh environments.
US manufacturers focus on NSF-approved raw materials. Lead-free formulations meet stringent drinking water regulations. Chlorine resistance addresses municipal water treatment concerns.
Size Variations and Compatibility
European sizing follows metric measurements exclusively. Common diameters include 20mm, 25mm, 32mm, and larger. Standardization across EU countries ensures compatibility.
American fittings blend metric and imperial sizing. Half-inch, three-quarter-inch, and one-inch nominal sizes remain popular. Transition adapters bridge measurement system gaps.
Quality Control Approaches
European manufacturers implement comprehensive quality management systems. ISO 9001 certification provides process oversight. Third-party testing validates performance claims regularly.
American producers emphasize field performance validation. Real-world testing in diverse climates informs product development. Customer feedback drives continuous improvement initiatives.
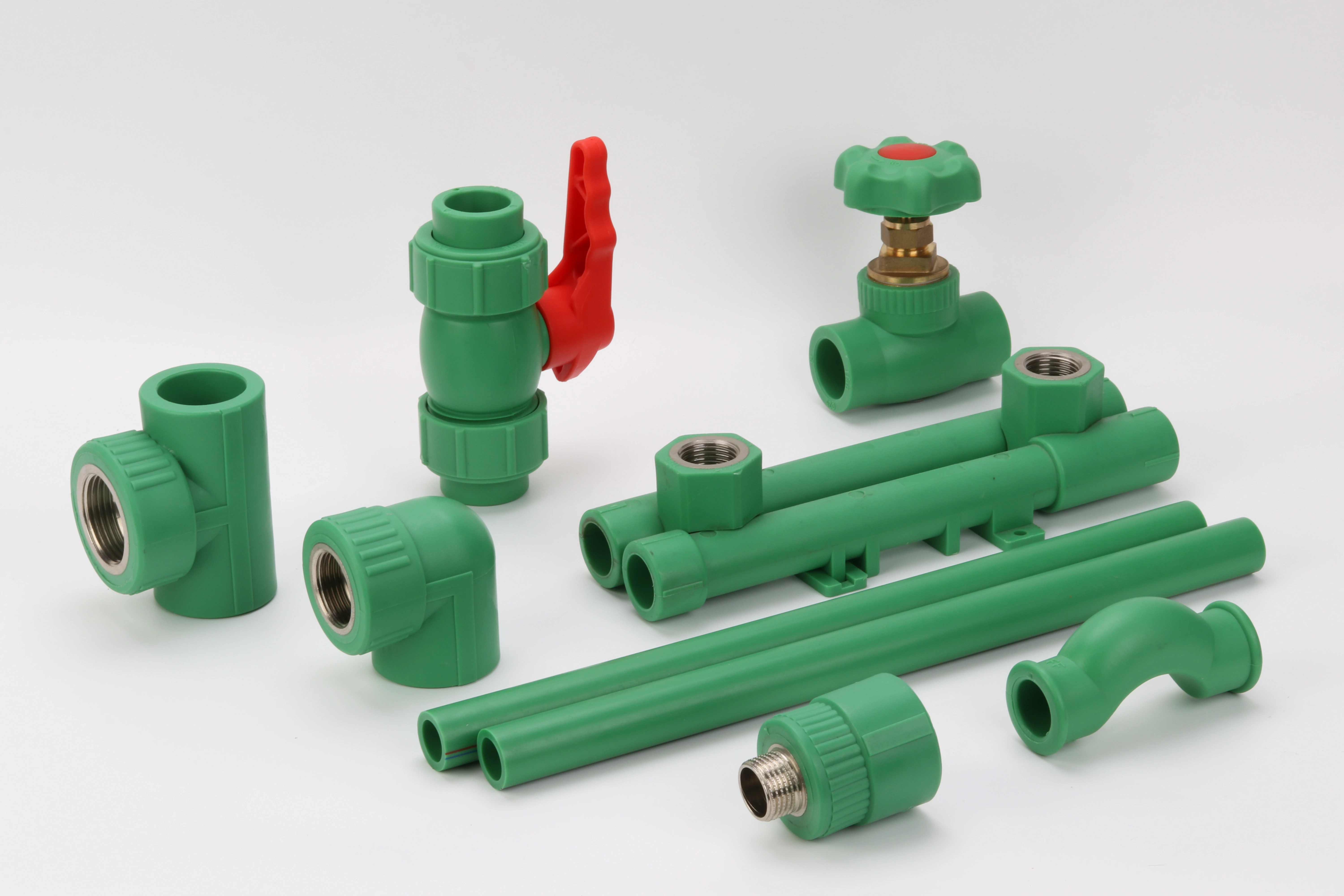
Installation Requirements
European installation practices require certified fusion equipment. Technician training programs ensure proper joint formation. Temperature monitoring prevents installation defects.
American installations allow more flexibility in connection methods. Mechanical joints supplement fusion welding options. Field conditions often dictate installation approach selection.
Cost Considerations
European PPR fittings typically command premium pricing. Higher manufacturing standards justify increased costs. Long-term reliability offsets initial investment differences.
American fittings compete in price-sensitive markets. Volume manufacturing reduces per-unit costs. Regional suppliers offer competitive alternatives to imported products.
Performance in Different Climates
European designs account for moderate temperature variations. Thermal expansion coefficients suit continental climate patterns. Freeze-thaw resistance receives engineering attention.
American fittings handle extreme temperature swings. Desert heat and arctic cold challenge material properties. UV degradation resistance matters in sunny climates.
Market Availability and Support
European suppliers maintain extensive distribution networks. Technical support includes installation guidance. Warranty programs back product performance claims.
American distributors focus on rapid delivery schedules. Local inventory reduces project delays. Technical assistance emphasizes practical application support.
Choosing the Right PPR Fittings
Project specifications determine optimal PPR fitting selection. Consider operating conditions, pressure requirements, and temperature ranges. Installation expertise availability influences connection method choices.
Budget constraints may favor regional suppliers. Performance requirements might justify premium European options. System compatibility ensures long-term operational success.
Professional consultation helps navigate these differences effectively. Experienced suppliers provide valuable guidance for specific applications. Quality installations depend on proper product selection and skilled installation practices.
Recent Comments