Table of contents
隐藏
1. Introduction: The Critical Role of Quality Assurance in European PPR Pipe Distribution
- Explain why quality is non-negotiable in European markets (strict regulations, safety standards, and end-user expectations).
- Highlight that distributors act as gatekeepers between manufacturers and clients, balancing compliance, performance, and profitability.
- Teaser: Uncover the 5-step framework European distributors use to guarantee PPR pipe quality.
2. Step 1: Adherence to Stringent European Standards & Certifications
- Core Standards:
- EN 12201 (PPR pipe systems for water supply).
- EN 10208 (pressure testing) and EN ISO 1461 (galvanized coating for steel components, if applicable).
- Certifications to Look For:
- CE Mark (mandatory for EU market access).
- KTW (Germany, for potable water safety), WRAS (UK), or NSF/ANSI 61 (for export to North America).
- Case Example: A French distributor refusing non-CE certified pipes during a 2023 customs audit.
3. Step 2: Rigorous Supplier Audits & Factory Evaluations
- Pre-Approval Checks:
- ISO 9001:2015 certification for quality management systems.
- On-site audits of production lines (e.g., extrusion machines, material storage, and testing labs).
- Red Flags:
- Lack of traceability for raw materials (e.g., no batch records for PPR resin suppliers like Borealis or LyondellBasell).
- Inadequate testing equipment (e.g., no pressure cycling or heat resistance chambers).
- Best Practice: A Spanish distributor using third-party inspectors (SGS, Bureau Veritas) for unbiased evaluations.
4. Step 3: Material & Product Testing Protocols
- Raw Material Testing:
- Melt flow rate (MFR) to ensure PPR particle consistency.
- Density and thermal analysis (DSC) to verify copolymer composition (e.g., PPR Type 3 for high-temperature resistance).
- Finished Product Testing:
- Hydrostatic pressure tests (1.5x working pressure for 1 hour).
- Impact resistance (e.g., -20°C drop test for cold climates).
- Long-term creep rupture testing (to confirm 50-year service life per EN 12201).
- Documentation: Requiring COA (Certificate of Analysis) and test reports for every shipment.
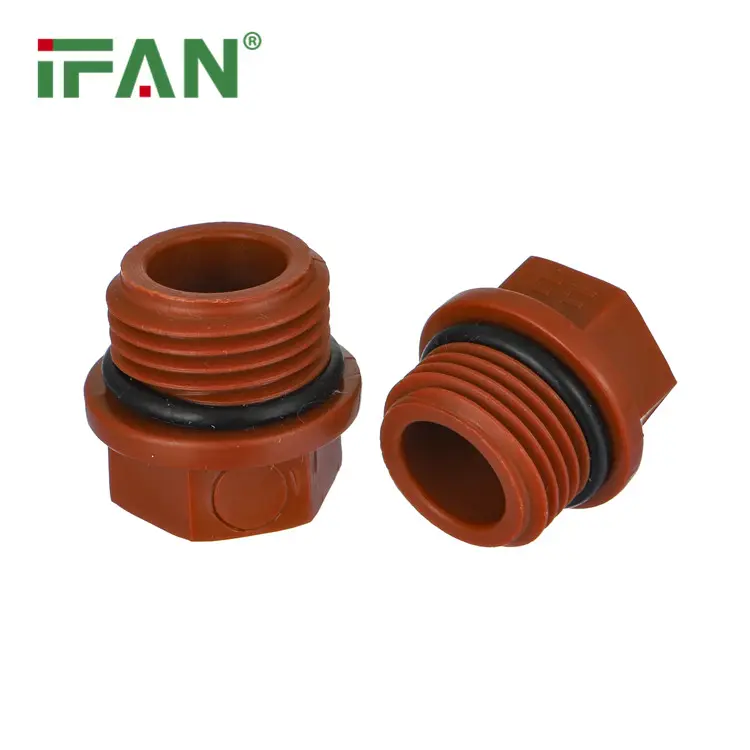
5. Step 4: Supply Chain Traceability & Compliance
- Lot Numbering Systems:
- Tracking pipes from resin purchase to installation via unique batch codes.
- Example: A German distributor using blockchain to map a 2024 PPR pipe shipment from China to Munich.
- Risk Mitigation:
- Avoiding “grey market” products (unauthorized re-exports without regional certifications).
- Storing pipes in climate-controlled warehouses to prevent UV degradation or physical damage.
6. Step 5: Post-Sales Quality Monitoring & Feedback Loops
- Field Performance Data:
- Collecting installer feedback on joint integrity, ease of fusion, and long-term leaks.
- A Dutch distributor reducing warranty claims by 40% after prioritizing suppliers with <0.5% field failure rates.
- Continuous Improvement:
- Regularly updating supplier scorecards based on quality metrics (e.g., defect rates, certification validity).
- Collaborating with manufacturers to refine products (e.g., adding UV stabilizers for outdoor installations in Southern Europe).
7. How to Partner with Reliable European PPR Pipe Distributors: A Buyer’s Guide
- Checklist for Importers/Buyers:
- Ask for a full list of current certifications and their expiration dates.
- Request access to supplier audit reports and test data.
- Verify traceability through sample lot number lookups.
- Why It Matters: Non-compliant pipes can lead to fines (up to €50,000 in Italy for WRAS violations) or project delays.
8. Conclusion: Quality as a Competitive Edge in European PPR Markets
- Reinforce that quality assurance isn’t just a checkbox—it’s a strategy to build trust, avoid penalties, and win long-term clients.
- CTA: Connect with [reliable PPR pipe suppliers](link to your company’s European certification page) who follow these standards.
Recent Comments