1. Introduction
Understanding the compatibility of PPR pipe fittings with other materials is critical for engineers, contractors, and facility managers. This guide will clarify key compatibility factors, common applications, and solutions for mixed – material systems.
2. Basic Principles of PPR Compatibility
2.1 Material Properties
PPR (Polypropylene Random Copolymer) has distinct thermal expansion coefficients and chemical resistance. These properties affect how it interacts with metals like copper or steel, and other plastics such as PVC or PE.
2.2 Connection Methods
Compatibility often depends on jointing techniques:
- Mechanical fittings: Forged brass or stainless steel adapters create transition points
- Electrofusion welding: Specific to PE – based materials
- Threaded connections: Require sealing tapes for metal interfaces
3. Commonly Compatible Materials
3.1 Copper Pipes
- Transition solutions: Use brass compression fittings
- Best practices: Always use dielectric unions to prevent galvanic corrosion
- Case study: A Singapore high – rise project reduced corrosion incidents by 40% using this method
3.2 Stainless Steel Pipes
- Recommended fittings: 316L stainless steel transition adapters
- Performance benefit: Maintain pressure ratings up to 16 bar
- Industry standard: Compliant with ASME B31.3 process piping requirements
3.3 PE Pipes
- Direct compatibility: Through electrofusion couplers
- Temperature range: Operate safely from – 20°C to + 95°C
- Municipal example: Beijing water authority’s 2024 pipeline upgrade project
3.4 Composite Pipes
- Hybrid systems: PPR – lined steel pipes for corrosive environments
- Pressure testing: Successfully passed ISO 13923 cyclic tests
4. Incompatible Material Combinations
4.1 PVC Pipes
- Chemical incompatibility: Chlorinated PVC may react with PPR under high temperatures
- Failure risks: Joint leakage after 18 – 24 months in hot water systems
4.2 Cast Iron Pipes
- Thermal expansion mismatch: Causes stress fractures in seasonal temperature variations
- Alternative solution: Use rubber gasketed mechanical couplings instead
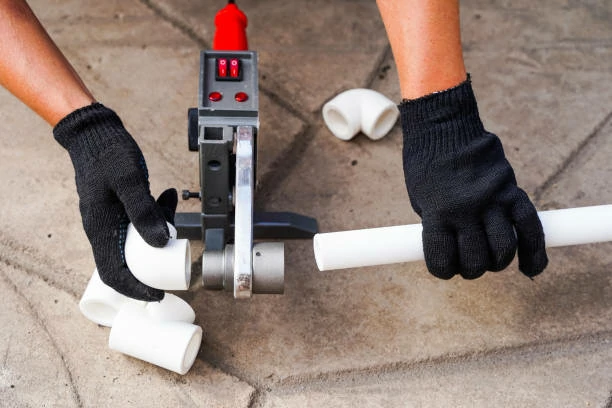
5. Professional Compatibility Solutions
5.1 Material Testing Services
Our ISO 17025 certified lab provides:
- Hydrostatic pressure testing
- Thermal cycling analysis
- Chemical resistance profiling
5.2 Custom Adapter Solutions
We offer:
- Threaded brass adapters with PPR liners
- Grooved couplings for fire sprinkler systems
- Custom – designed transition fittings for special projects
5.3 Compatibility Database
Access our online tool to check material combinations:
- Real – time compatibility reports
- Installation torque recommendations
- Maintenance interval calculators
6. Yifan Pipeline’s Compatibility Expertise
As China’s leading PPR system manufacturer:
- All fittings meet EN 12201 and NSF 61 standards
- 15 – year warranty on transition fittings
- 24/7 technical support for mixed – material projects
7. Case Study: Mixed – Material Hotel Project
Challenge: A 5 – star hotel in Dubai required connecting PPR with existing copper pipes
Solution:
- Conducted material compatibility analysis
- Deployed our patented brass – PPR transition fittings
- Implemented dielectric isolation technology
Result:
- Zero leaks after 3 years of operation
- 28% reduction in maintenance costs
8. Best Practices for Mixed Systems
- Always use certified transition fittings
- Install expansion loops for temperature – sensitive applications
- Conduct pressure testing at 1.5x operating pressure
- Maintain proper pipe support spacing
9. Conclusion
While PPR fittings can integrate with multiple materials when properly designed, professional engineering is critical. Visit ifanultra.com to explore our comprehensive range of compatible solutions or contact our experts for custom project support.
Recent Comments